Learn About the Benefits of a Trailer Mudguard
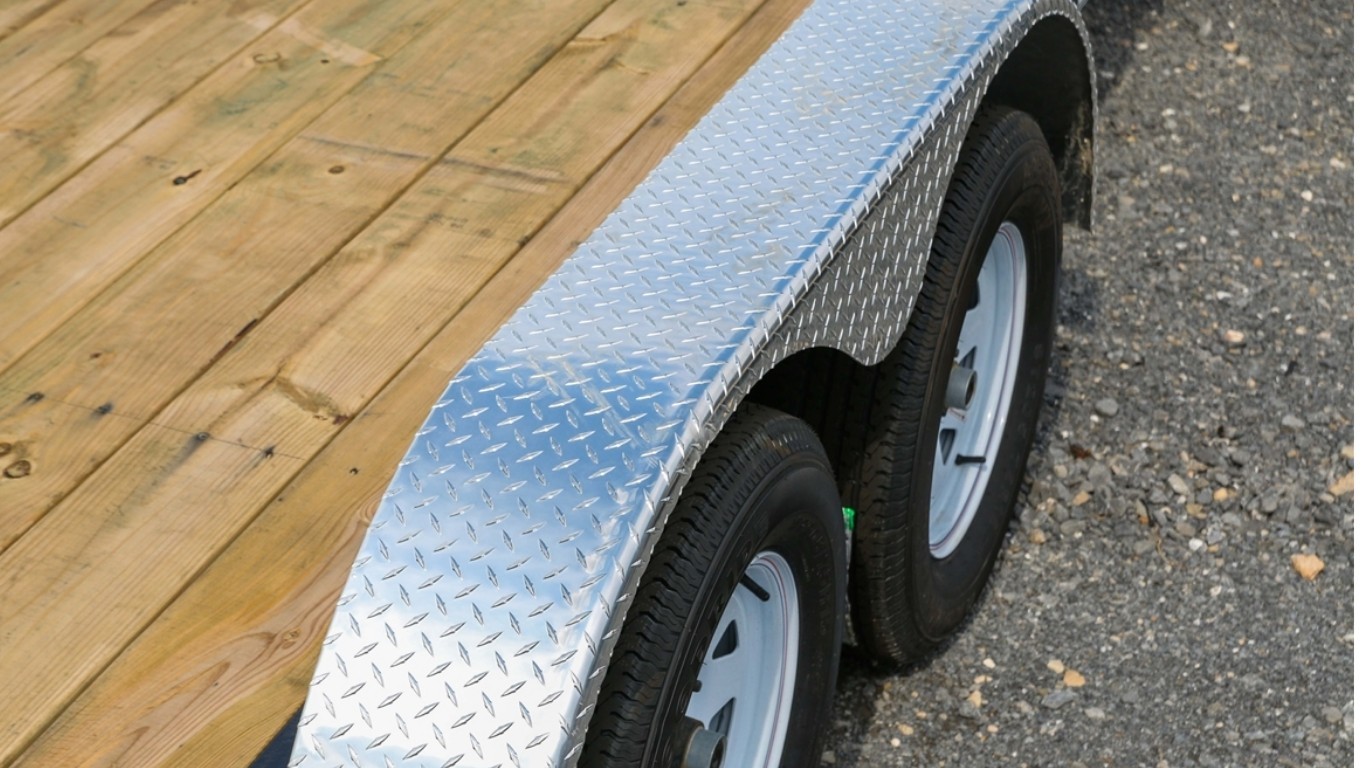
It's common to install fenders on trailers and vehicles. The installation of truck and trailer fenders offers several benefits, including giving the owner the opportunity to personalize the vehicle. Obviously, fenders are more than simple decorations, let's take a look at some of their benefits and their uses.
Legal Requirements for Fenders
The specific operation of tractor-trailers and other large rigs is governed by strict laws that are in place to better protect smaller vehicles from potential hazards. As far as fenders go, a number of states already have some requirements. For example, the installation and use of offenders are governed by Arizona-specific rules. Combinations of water, gravel, or debris types must be diverted by guards, according to some state regulations.
Regardless of state regulations, it is good practice to install quality, safe, and durable trailer fenders. This is especially true for larger vehicles, but fenders have also (over the years) been a fashion statement for smaller vehicles.
Fenders Provide Protection
Protection is the main purpose of offenders, but they protect more than just mud. Also protects water, rocks, etc. They stop unsafe conditions and damage to other vehicles from flying debris lifted from trailer and truck tires. But they also prevent damage to the rig's landing gear. Salt, other ice-melting chemicals, and corrosive elements are also prohibited from contact with trailers and tractors due to the durable materials on the fenders.
Fenders Extend Life
With all the protection that fenders provide, it's no surprise that trailer and truck mechanical components last longer when fenders are used. And to ensure that the brackets holding the fenders are durable, not only are they adjustable and made of spring steel but for safety and security, the hangers used during installation have been tested many times.
What Materials Are the Fenders Made Of?
Steel fender
Steel fenders have been in widespread use since the inception of the trailer industry, and as such, are generally less expensive and available in a variety of sizes and styles. Steel also withstands dents, cracks, and other forces applied to them better than fenders made of other materials. However, they are much heavier and require more preparation before they are ready to be applied to a trailer. Steel fenders have a much higher chance of rusting and need to be painted to protect from the elements (especially if you're going with a boat trailer) and help prolong their life. Steel fenders absorb and hold paint very well, even if it's a simple clear coat, you'll want to do this before installing these fenders.
Aluminum fender
On the other hand, aluminum is more resistant to the elements and weather conditions than steel fenders. It is overall lighter, and if properly maintained, it will give you a longer life than steel and require less maintenance. However, aluminum is more prone to bending and breaking under pressure or weight than steel. Another big disadvantage of aluminum is that if you plan on customizing the fenders by painting to match your trailer, aluminum won't hold the paint very well compared to steel fenders even when prepared properly. It's also generally a more expensive option than steel and plastic fenders.
If you want to know more about trailer-related products, you can contact us.
Haway is a professional light trailer accessories manufacturer. We have been manufacturing and supplying trailer accessories since 2002. Our products are exported to Australia, New Zealand, Canada, the United States, and some European countries. Our factory produces a large number of trailer axles, torsion axles, trailer fenders, trailer jacks, boat trailer rollers, and brackets. It has advanced equipment such as a laser cutting machine, robot welding machine, CNC lathe, etc. We have advanced CNC lathes, laser cutting machines, robotic welding machines, punching machines, etc. An advanced laser cutting machine can cut 0.5mm-16mm steel plates. The advanced laser cutting technology makes the development of new products easier and greatly saves the customer's mold cost.